一、行业背景
风电发电机组中最主要的固定连接方式就是利用螺栓连接,成千上万的螺栓的质量直接影响风力发电机组运行的安全性和可靠性。由于风电螺栓规格种类多,数量庞大。因此,提供一种快速有效的螺栓服役质量检测方法是保障风力发电机组安全运行的重要手段。
二、风电螺栓的分类
风机发电机组构件大部分都是通过高强紧固螺栓连接紧固,主要构件部位在叶轮、偏航、塔筒等部位;风电螺栓按所在风机部位可分为塔筒螺栓、偏航螺栓、主轴连接螺栓、叶片螺栓(内外圈)等;按螺栓形状可分为内六角螺栓、外六角螺栓、双头螺柱等。
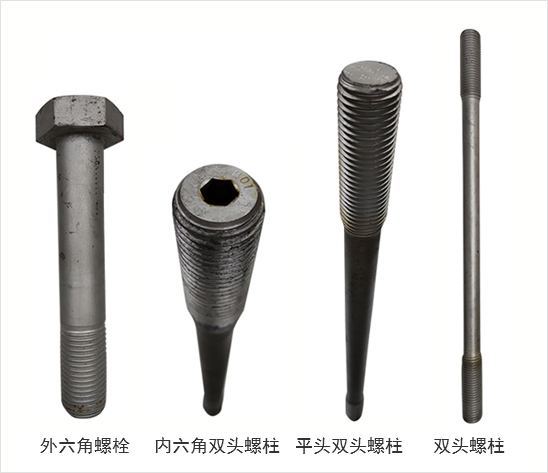
图1. 风电螺栓
三、风电螺栓的相控阵3D全聚焦(TFM)检测方法
图2. 相控阵全聚焦实时3D超声成像系统CTS-PA322T
CTS-PA322T系统配套风电螺栓专用探头,检测风电螺栓时只需按规定操作,把探头置于螺栓端部(两端均可)不需要移动探头等操作。CTS-PA322T系统便能够实时采集被检测螺栓内部所有信息,并实时输出被检测螺栓的3D检测图像。系统提供缺陷分析存储功能,能够对被检测螺栓内部缺陷进行准确定位、定量测量。
风电螺栓检测案例:
为了验证相控阵全聚焦实时3D超声成像系统CTS-PA322T探伤设备和检验探伤结果可行性,我们通过利用该设备的3D成像图与常规相控阵B扫图(线阵探头、菊花阵列探头)以及常规A扫图进行对比。
> 案例1:塔筒螺栓
该塔筒螺栓在螺纹处加工了两个2mm深的人工刻槽,检测结果图像如下:

图3. 塔筒螺栓的3D全聚焦检测图像
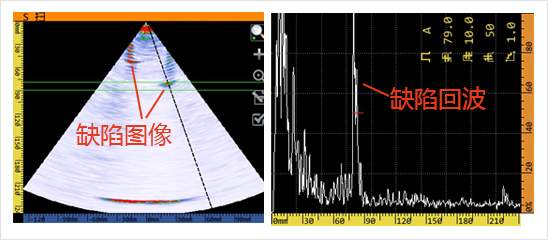
图4. 塔筒螺栓的常规相控阵检测图像
> 案例2:叶片螺栓
该叶片螺栓存在两个目视不可见的自然裂纹缺陷,检测结果如图:
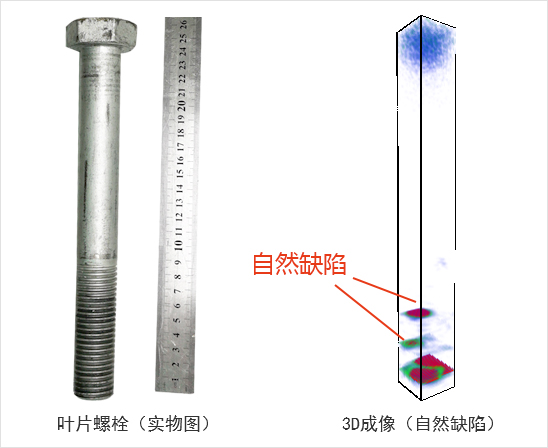
图5. 叶片螺栓的3D全聚焦检测图像
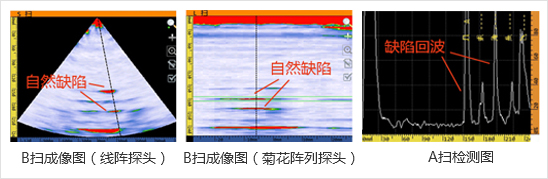
图6. 叶片螺栓的常规相控阵检测图像
> 案例3:叶片螺栓
该叶片螺栓加工了两个2mm深的人工刻槽,检测结果如图:
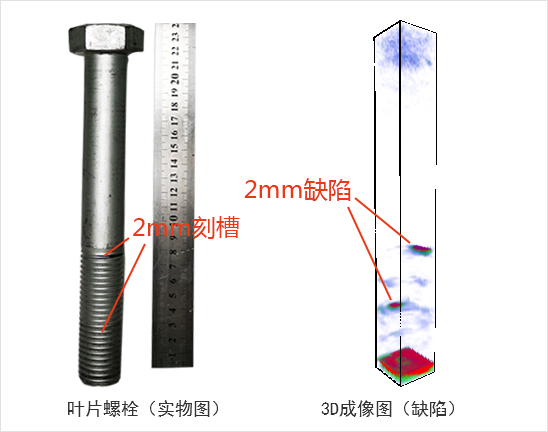
图7. 叶片螺栓的3D全聚焦检测图像
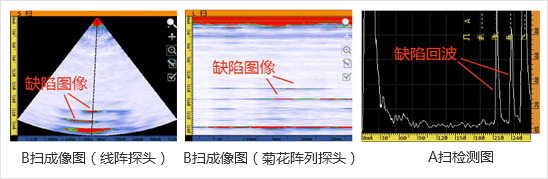
图8. 叶片螺栓的常规相控阵检测图像
> 案例4:内六角叶片螺栓
内六角叶片螺栓采用我司研制的内六角螺栓专用探头进行检测,该螺栓加工了2mm深的刻槽缺陷:
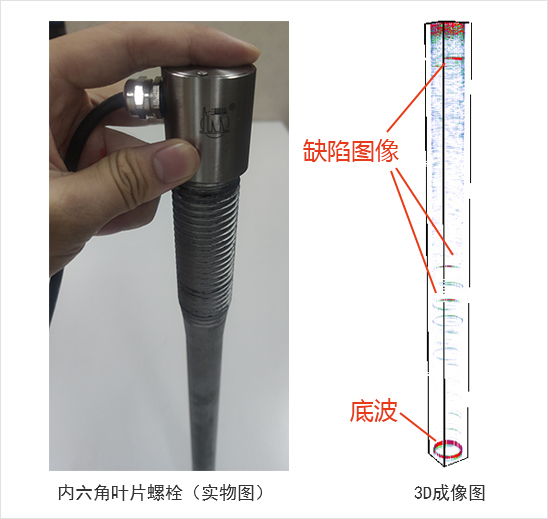
图9. 内六角螺栓的3D全聚焦检测图像
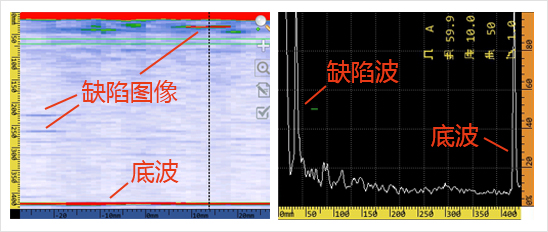
图10. 内六角螺栓的3D全聚焦检测图像
> 现场检测案例:M28×240叶片-变桨轴承内圈螺栓自然缺陷检测
在某风电场现场进行的1.5MW风机风电螺栓全检过程中,在叶片-变桨轴承内圈螺栓中发现了五根带较大裂纹缺陷的螺栓,并进行了螺栓的现场拆卸更换。在卸下的螺栓中,发现了一根在卸过程中断裂螺栓,一根出现明显裂纹以及三根肉眼无法识别裂纹缺陷。
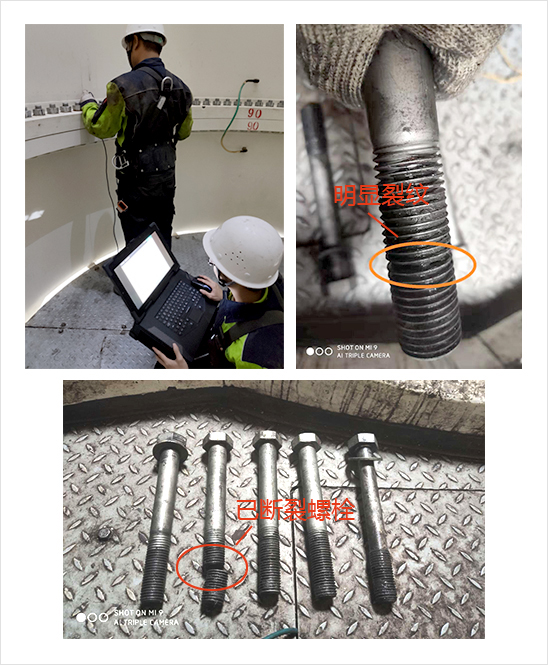
图11. 现场检出并卸下的带裂纹螺栓
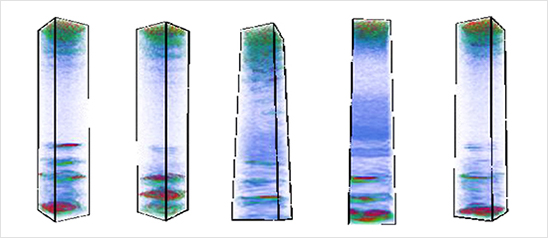
图12. 现场检测3DTFM成像图
四、风电螺栓的传统检测方法
螺栓的无损检测方法主要有超声、磁粉、渗透及涡流检测,但针对风电螺栓检测的在役性要求,便只有超声检测满足检测条件。而超声检测也可细分为常规超声检测和相控阵超声检测。
> 常规超声检测(UT):
常规超声检测主要采用小角度纵波探头对螺栓进行检测,并通过波形判断检测结果,此方法对检测人员具有一定的检测经验要求,且只适用于部分规格较小的外六角螺栓的检测。对于内六角螺栓、内六角双头螺柱及较长的螺栓则无法采用此方法,检测效率也相对较低,是风电螺栓在役超声检测中最不推荐使用的一种方法。
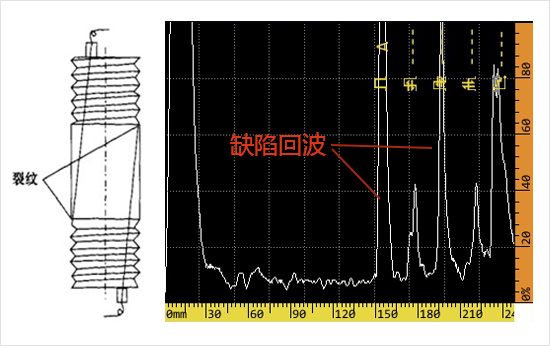
图13. 螺栓的常规超声检测
> 常规相控阵检测(PAUT):
常规相控阵检测的图像判断不同于常规超声检测的波形判断,检测结果的二维图像直观性有进一步地提高,可检范围更广,基本可覆盖小兆瓦风机螺栓的检测需求。
常规相控阵的目前采用的主要有两种扫查方式:一种是采用线阵探头进行扇扫或线扫成像检测(如图14),但此方法一次只能检测螺栓的一个切面,要想完整的检测整根螺栓至少需将探头进行旋转180度的扫查来实现全覆盖,从而降低了检测效率。
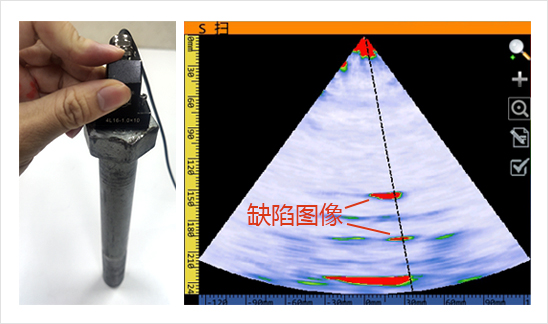
图14. 扇扫检测结果图
另一种方法则是采用菊花阵列探头来检测(检测结果如图15),采用该方法无需旋转探头,可提高检测效率。但是采用菊花阵探头检测的结果无法直观地体现裂纹裂深的情况,也无法检测螺栓内部缺陷,对探头与螺栓规格的尺寸匹配要求相对较高,但总体相较于常规超声检测,常规相控阵的检测结果更直观,可检范围更广,基本可实现风电螺栓的检测。
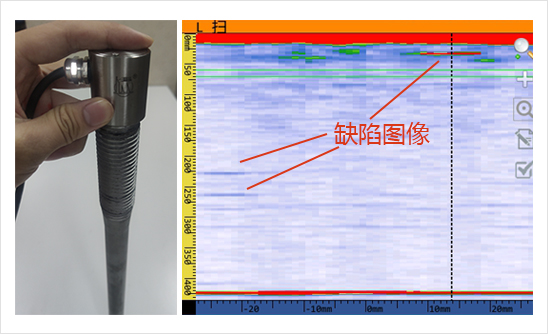
图15. 菊花阵线阵检测结果图
综上,螺栓的传统检测方法,常规超声和常规相控阵均可以进行在役检测。但是对检测人员要求高,人为因素影响比较大,而磁粉和渗透则不利于现场在役检测。
3D全聚焦技术的优势:
在三维空间内从各个不同空间角度采集被检测工件内部的缺陷信息,信息采集更充分,螺栓内部缺陷一览无余,成像直观可靠,避免缺陷漏检。
无需移动探头,可实现对螺栓整体的实时3D成像。且可旋转观察,检测结果更直观,系统提供缺陷分析存储功能,能够对被检测螺栓内部缺陷进行准确定位、定量测量。
一根螺栓检测时间不到2秒钟,检测效率高。