1. Demand background of aircraft wheel inspection
Due to the high specific strength of (α + β) titanium alloy it is still widely used in fan components. The defects of solidification segregation and hydrogen embrittlement are inevitable in the forming process of this kind of titanium alloy. The investigation conclusion of the Sioux City air crash is that the hard α phase in the forming process of the titanium alloy disc material leads to the rupture of the disc before the "safe life" is reached. Therefore from the perspective of improving the overall safety level of the engine in the process of fan disk design and life determination it is necessary to evaluate the failure probability of hard α equivalent defects in the life cycle of the wheel disk which is also one of the compliance points that must be indicated when the engine airworthiness certification.
2. Research on the inspection of aircraft wheel
A domestic university took the titanium alloy wheel disc with hard α inclusion as the research object combined with the low-cycle fatigue crack growth test of high-speed rotary table and Guangdong Goworld Co.Ltd ultrasonic instrument branch to carry out the research on the crack growth characteristics of the titanium alloy wheel disc. The main research work is as follows:
1. Design and preparation of titanium alloy wheel test piece. The preparation method and burial method of hard α inclusion are proposed to determine the burial position of hard α inclusion.
2. The vertical rotation tester was used to carry out the low-cycle fatigue test of titanium alloy wheel which actively promoted the crack growth and simulated the actual in-service situation.
3. Using phased array TFM real-time 3D ultrasonic imaging system CTS-PA22T developed by Guangdong Goworld Co.Ltd ultrasonic instrument branch regularly inspect the imaging records of the buried hard α inclusions and make quantitative measurements to study the growth rule of the occurrence and expansion of hard α inclusions .
3. Scheme of 3D total focus detection system for aircraft wheel
3.1 Mechanical system
3D total focus detection mechanical system of aircraft wheel
The overall dimension of mechanical system equipment is 600mm in height 600mm in length and 600mm in width. The outer wall of the water tank adopts transparent acrylic which is convenient to see the detection position of the workpiece. The height of the water tank is 270mm and the working storage capacity is about 85 L. There is a circular boss at the bottom of the water tank which can locate and fix the turbine disk. According to the different specifications of the detected turbine disk the circular boss can be replaced. The detection phased array probe vertically moves up and down by a motor the depth of the probe is automatically detected in place and closed-loop control is realized by proximity switch.
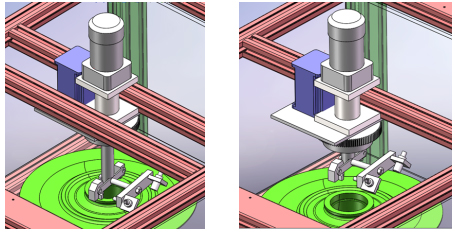
Detection status and end status
The detection tooling uses the principle of balance structure one side is the detection probe and the other side is the proximity switch. During the detection the probe automatically drops to the designated position and triggers the proximity switch which can effectively achieve the automatic positioning of the detection probe. When the probe reaches the specified depth another motor is started and the probe is driven by gear to scan the circumference. In the detection of the top surface of the turbine disk the detection probe is a certain distance away from the turbine disk.
Schematic diagram of aircraft wheel top surface inspection
When the detection probe is placed on the inclined surface of turbine disk for detection 3D total focus detection with a single probe or TOFD detection with double probes can be achieved.
Schematic diagram of turbine disk bevel inspection
3.2 Imaging system
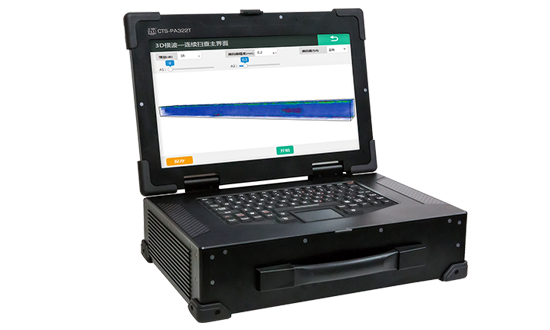
CTS-PA22T 3D TFM imaging detection system
3.3 Inspection conclusion of aircraft wheel
The height of the hard α inclusion defects was detected to be 7.4mm and the natural crack defects developed close to the surface.

2D-TFM inspection imaging
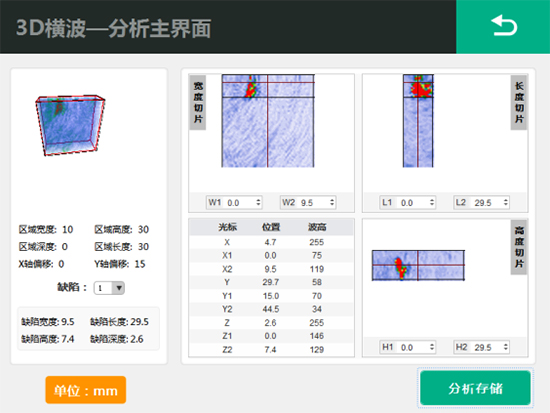
3D-TFM inspection imaging